Value Engineering: Meaning, Benefits & Stages
Value engineering is a systematic method used to improve the value of a product or project. One of the main focuses of value engineering apart from reducing costs is to ultimately achieve better value for the client, without compromising the function of a product. This involves searching for substitute materials and methods whilst ensuring there is a balance between cost, function, and value.
Figure 1 - The relationship between cost, functionality, and value.
The notion of value engineering was first developed and championed by Larry Miles at General Electric in 1947, shortly after the Second World War. Substitutes were needed due to shortages of raw materials, components, and manufacturing labour. This soon turned into a systematic process, looking for alternatives that could deliver more value whilst reducing costs and maintaining consistent quality.
To maximise cost efficiencies, value engineering is most effective when taken as a guiding principle followed right from the outset of the planning and design. The figure below won’t be news to you if you’ve been closely involved in the management of a construction project: it clearly shows how the cost of change increases whilst the impact of change decreases throughout any given project. The upshot? In almost all cases, decisions that are geared towards value engineering are more impactful and cost-effective if made early on (see Figure 2). Changes made late in the construction stage may even have a negative impact on value.
Figure 2 - Value and cost impacts as a result of change at different stages of a construction project.
This guide offers a look into what value engineering is, the benefits, and the formula used to calculate opportunities and cut costs in the construction of a project. Along the way, we will explore the importance of value engineering in construction and the 6 key stages to understand the process, before considering the challenges of value engineering and ways to overcome them.
Looking for something in particular? Use the links below to navigate straight to it:
- What is value engineering?
- The importance of value engineering
- Value engineering formula
- The 6 stages of value engineering
- Value engineering challenges
- The form of construction contract affects value engineering
- Early contractor involvement encourages value engineering
- Case study: value engineering with pavement optimisation
- How Tensar can help reduce costs through value engineering
Need help with value engineering for your next project?
Get in touch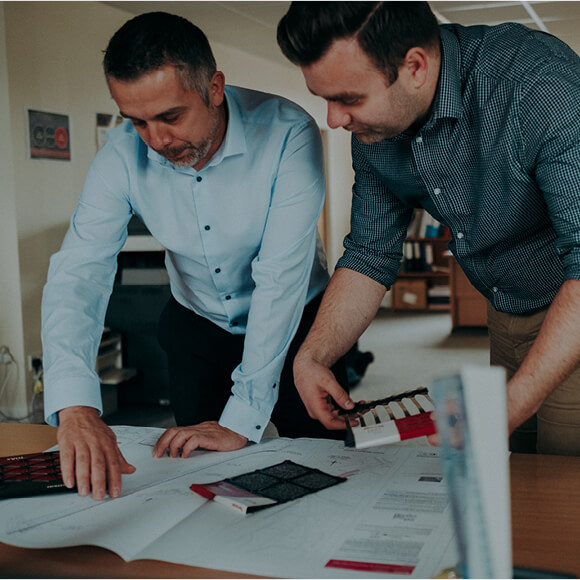
What is value engineering?
Value engineering in construction is a method used to identify opportunities for changes in the project to reduce costs for the client while making sure that it ultimately functions as effectively as originally planned, meeting or exceeding the needs of the client.
There are 6 key phases of value engineering: informational gathering, brainstorming, evaluating, developing plans, presentation, and implementation. These steps ensure all cost elements throughout the project cycle are analysed, offering multiple opportunities when presenting to stakeholders. The value is calculated as a ratio of function to cost, ensuring the best outcomes are achieved while reducing costs.
Value engineering can improve various parts of the project, including:
- Material substitution
- Techniques used in construction
- Design optimisation
- Waste reduction
- Regulatory compliance
- Water efficiency
- Technological innovation
- Site management
Value analysis vs value engineering
When comparing value engineering vs value analysis, there are a few key differences to consider:
- Value engineering focuses on finding cost savings in the design and planning phase, and identifying cost-saving opportunities before the production and construction of a project begins.
- Value analysis, on the other hand, is about evaluating existing products and systems, and finding opportunities to improve their cost efficiency to maximise profits. It also focuses on not compromising on quality when reducing costs.
The importance of value engineering
When carried out effectively, value engineering is a win-win for all involved. With the many benefits of value engineering, there’s never been a more important time for the construction industry to utilise this process. Whether it’s cost reduction, enhanced project efficiency, or environmental impact, there are many reasons to consider a mindset shift toward a more value-driven approach. Let’s unpack these in more detail. This section will highlight the importance of value engineering in construction.
Cost reduction
Reducing costs is the most immediately apparent benefit of value engineering in construction. By looking into and identifying opportunities to save small sums throughout the full lifespan of a project, overall costs can be cut without affecting the overall quality and performance. This includes the materials used, production processes, prefabrication, and equipment, to name just a few areas.
Figure 3 - Using the T-Value method with Tensar InterAx geogrid on this working platform for the Stoneleigh Park project saved an estimated £250,000 in construction costs and 15 days in construction time.
Enhanced project efficiency
Another byproduct of the value engineering mindset is that it naturally results in projects running more efficiently. To stop costs from spiraling out of control, project timelines need to be clearly set out, and teams need to stick to them as closely as possible – so productivity becomes a key focus. There’s also an imperative to design for value, part of which involves making better use of resources.
Environmental impact
Can a construction material be more cost-effective and better for the environment than the alternatives? In some cases, yes. Recycled aggregates for example, can be used as backfill for retaining structures and in road construction when combined with stabilising geogrids. One benefit of this is that it reduces the need to source newly extracted primary aggregates, which can be costly. Reusing construction and excavation materials in this way minimises transport costs too, helping to lower the overall carbon footprint of a construction project.
Figure 4 - After Eastleigh Railway depot encountered weaker subgrade conditions, Tensar InterAx geogrid was used to create a stable working platform in the construction phase – all whilst cutting down carbon emissions by 35%.
Improved safety
Safety issues in the construction process can be identified through value engineering. Materials and designs have to meet the required safety standards to be approved, however, safety can sometimes be improved. If any elements have been missed previously, this is the perfect time to ensure all safety measures are in place.
Discovering any possibilities to improve the safety of a project early on in the design phase can not only create safer designs but also lead to fewer accidents in the workplace. An example would be the safety benefits from reducing the volume of aggregate materials imported to and from a site. Tensar value engineered designs for roads require less aggregate, this reduces the number of vehicle movements on site and on local roads, lowering the potential for collisions as well as disruption on local roads.
Customer satisfaction
When evaluating the design phase through value engineering, all client-specific needs should be met. Building trust between the client and project team is key to maintaining a strong relationship and increasing the chances of future collaborations. It can improve the overall customer experience and satisfaction. Transparent communication during the value engineering process can make clients feel that their objectives are being prioritised with the best possible outcomes.
Value engineering formula
Once you understand the benefits of value engineering in construction, to help decide whether there is a higher value solution compared to the original design, this may be calculated using the following formula:
Product value = functionality / cost
The cost is the amount the client spends on the item over the entire lifecycle, while the function is the quantitative evaluation of the item and the task it was designed to do. By optimising the function and reducing the cost, you can increase the overall project value. It's highly important to balance the two to achieve a cost-effective product that doesn’t compromise on quality or performance.
Understand how Tensar geogrids support value engineering with our Tensar+ software
Sign up for free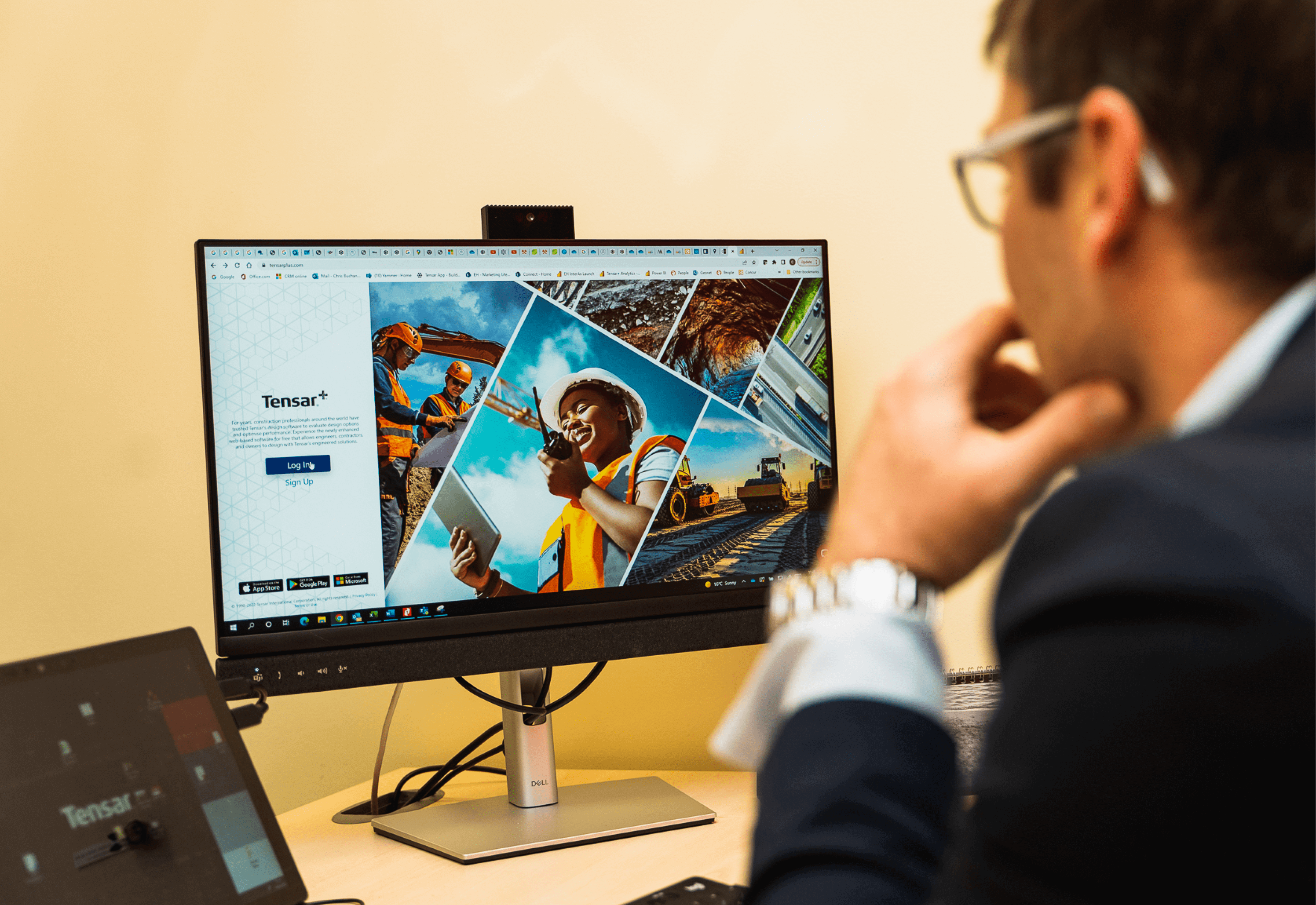
The 6 stages of value engineering
We’ve already touched briefly on the history of value engineering, which is rooted in the ideas first put forward by Larry Miles at General Electric in 1947. He came up with 6 clearly defined stages of value engineering: information gathering, brainstorming, evaluation, development, presentation, and implementation. The information gathering stage will enable the required functionality to be analysed and clearly defined. For construction projects, this is an important feed into the brainstorming and we have added it as an additional stage in the process, (See Figure 7 below). Read on for a detailed breakdown of each of these steps and how they could apply to your project.
1. Information gathering
The value engineering process begins by gathering information from analysing every part of a project lifecycle. All elements that contribute to the overall cost should be included. For instance, you’ll want to look into the costs associated with design, material selection and sourcing, offsite manufacturing, construction methods, future maintenance and finally, demolition and recycling potential.
Expectations regarding time and labour should also be considered. Even the basics of the project such as who will be using the asset and what is to be achieved overall from the project are part of the information gathering stage.
2. Brainstorming
To reduce costs in the lifecycle of a project, brainstorming ideas is key to helping think of more efficient ways of functioning. It is essential to define the required functionality that will fully meet the client needs over the full life cycle. By analysing the function process, value engineering can also be used to look into how each function benefits the client. This stage is essential for creative thinking and identifying new ways to improve the current life cycle of the project.
It can prove useful to seek external support during the brainstorming phase, as a fresh pair of eyes will often spot missed opportunities. If you’re planning a project with a focus on geotechnical engineering, reach out for a free value-engineered solution or our expert input on how to achieve cost efficiencies.
3. Evaluating
After the brainstorming is complete, ideas are taken further through evaluation. For each alternative, an evaluation of the advantages and disadvantages are compared to the current ways of functioning. If there appear to be more advantages to a new idea, then this may be taken forward.
For example, in a road construction project you could value engineer the pavement design by considering a mechanically stabilised subbase or base layer, to increase design-life or enable a reduction in pavement thickness, saving on materials and time.
Alternatively using Tensar’s value engineering solutions to stabilise the pavement foundation can increase load bearing capacity, and reduce the amount of materials used in a project. Our Tensar geogrids not only enhance pavement performance but can also cut long-term maintenance costs.
Figure 5 - Axbridge Road needed a capping layer over weak ground to accommodate construction traffic. Using Tensar geogrids saved £86,000 in construction costs, improving structural integrity, and preventing road cracking – ultimately saving on future maintenance.
4. Developing plans
The next stage is the development phase, where the alternative plans are fleshed out more thoroughly after an initial analysis. Value engineers will develop the thinking behind these elements and subject them to more detailed assessment. Designs, specifications, quantities, and costings will be prepared.
Return on investment (RI) should be kept front of mind at all times as plans develop to ensure that there will be a strong potential for cost savings; at the same time, you should continuously assess whether or not the proposed change would have an impact on functionality, and quantify this where possible. Remember that the ideal outcome of this stress testing is to improve value – which means reducing costs, but not at the expense of quality or functionality.
During the planning of the Ash Tree Park housing estate in Kendall, our design engineers spotted an opportunity to help Story Homes increase the value of the development through the use of an innovative reinforced soil slope solution. Not only did this increase development space for homes and gardens, but it also delivered substantial time and cost savings for the company.
Figure 6 - Tensar’s TensarTech NaturalGreen system, incorporating site-won soil has increased space for homes and gardens built on two levels at Ash Tree Park in Kendall
5. Presentation
Now that all the information has been gathered and analysed with potential outcomes, the next step is for the value engineering team to present the proposed change to key stakeholders. Ideas should be backed up by meaningful numbers with a timescale and project impact statement. Stakeholders may want to add or amend suggestions, and having multiple options available is better to ensure at least one is approved.
6. Implementation
Once the project change has been approved, the implementation stage begins. In the implementation phase, engineers and quantity surveyors need to track and monitor the changes to ensure they’re achieving the intended impact.
Monitoring and tracking are also useful for discovering ways to further improve and adapt accordingly to the results. This will ultimately improve the return on investment and the success of a project.
Figure 7 - The seven stages of value engineering on a construction project
Challenges of value engineering
Value engineering is about more than just reducing costs. It’s also a matter of finding alternative solutions that provide the same function and quality, which comes with its own set of challenges.
Balancing cost with quality
Reducing costs while ensuring that this doesn’t affect quality is no walk in the park. Over-prioritising cost savings at the expense of functionality can of course lead to issues with performance and longevity. It’s important to investigate the potential ramifications of any process or material change that’s proposed before arriving at a decision – and to keep in mind that maintenance down the line can ultimately prove more costly than selecting a more expensive, better-engineered solution in the first place.
Road engineering is an apt example: when pavements are constructed without sufficient strength and stiffness, fatigue-related cracking can occurdue to traffic loads over time, that severely reduces the pavement life. This may also lead to the formation of potholes that cost substantial sums in repairs. The development of fatigue cracking could be avoided through an improved initial pavement design. In this scenario, incorporating geogrids such as Tensar InterAx into the road foundation layers wouldn’t excessively inflate construction costs, but would extend pavement life, and producing significant cost savings in the long term.
Figure 8 - The use of Tensar InterAx geogrid generated immediate cost savings of £177,000 at North Heybridge Estate Road – with cost efficiencies compounding over time due to reduced road maintenance requirements.
Time-consuming
The whole process of value engineering can be time-consuming, especially in the analysing and development phase. Finding alternatives to the initial plan if it doesn’t deliver value takes time. This can require the involvement of project stakeholders, who need to review the designs, materials, and process in thorough detail. Gaining the acceptance of the client via their project representatives can also take a long time.Figure 9 - Using Tensar geogrids at Whitelee Wind Farm eliminated the need for time-consuming and costly peat excavation and aggregate replacement – with overall aggregate volumes reduced.
Resistance to change
Clients may not be willing, or contractually able to agree to changes, especially within organisations that have well-established processes or partnerships in place. To prevent such resistance from bringing proceedings to a halt, it’s best to workshop multiple alternatives to any proposed change and come armed with hard evidence of the benefits before presenting your ideas.
The effect of construction contracts on the value engineering process is explored below.
Experience
To successfully implement new cost-efficient alternatives without compromising on quality, teams need to be highly skilled and experienced. Value engineering can be complex and having a deep understanding of the construction process and cost management is essential. Without this knowledge and understanding, it can be harder to maintain a balance between cost, quality, and functionality. Construction companies are often best placed to provide this expertise.
The form of construction contract affects value engineering
Construction projects can benefit from the expertise and capabilities of the construction company carrying out the works. They can bring their experience of materials and construction methodology to play and offer value engineered alternatives to the original scheme design. However, they need an incentive to spend time and resources developing value engineered alternatives. If the form of construction contract does not enable value engineering to take place and importantly, provide a mechanism for the sharing of any benefits between contractor and client, then the opportunity for improved value will be lost.
The two most common construction contracts used in the UK are those of Joint Contracts Tribunal (JCT) and New Engineering Contract (NEC). The JCT contract is often used for building projects where roles and responsibilities of all parties are clearly defined and follow traditional lines. The NEC contract, more commonly used for civil engineering works, promotes a more flexible and collaborative means of working between parties. There is a proactive approach to the management of risk, which is well better suited to large complex projects.
There are six contract options supported by the current NEC Engineering and Construction Contract (NEC4 ECC). Value engineering is enabled within most of these options.
Option A -NEC4 ECC Priced contract with activity schedule
A version of ‘lump-sum’ fixed price contract, where the contractor commits to a price to carry out the works as designed and specified, and this is what the client will pay. In some cases, price adjustment through indexation is agreed at the outset. However, the core clauses of the contract allow the contractor to offer value engineered alternatives, providing the change is accepted and brings about a reduction in the amount to be paid by the client.
Option B – NEC4 ECC Priced contract with bill of quantities
In this version the contractor puts unit prices against each item in a list of materials and services. The contractor’s payment is calculated based on measured work completed, using the unit costs for each item measured. The same scope for value engineering detailed above for Option A, exists for Option B
Option C – NEC4 ECC Target contract with activity schedule, and Option D with Bill of quantities
The contract sets an initial target price for the works which is adjusted based on events. The contractor is paid in instalments throughout the project on a cost-plus-fee basis. Significantly, any cost savings or cost overruns are shared between the client and contractor in pre-defined share ranges. The contractor is encouraged to make value engineered proposals with the cost saving benefits shared with the client.
There are many examples where Tensar has engaged with the contractor to develop value engineered alternatives that have been accepted by the client, delivering cost savings shared between contractor and client.
Early contractor involvement encourages value engineering
We saw in Figure 2 that the greatest cost impact from value engineering is going to come from changes made during the early stages of a project, preferably in the planning and design stages. The value of contractor input at this stage is well understood but is not possible by traditional forms of contract and working arrangements. One form of contract that enables this early collaboration is known as ‘Early contractor involvement.’
NEC4 ECC can facilitate early contractor involvement by enabling a single contract with two stages. During the first stage the contractor joins with the project team to develop the scope, detailed design, and price of the works. Value engineering occurs during that early stage for the benefit of the client, and the contractor is compensated for their valuable input.
Case study: value engineering with pavement optimisation
In the Orchard Place housing scheme, The Borough Council of King’s Lynn and West Norfolk and housing developer Lovell needed to mitigate differential settlement of temporary access roads and paved areas over weak and variable ground. Tensar geogrids were used to mechanically stabilise aggregate layers of unsurfaced roads, and Tensar designed temporary access roads that could be safely used as foundations for permanent roads.
Tensar value engineering helped save £64,000 on flexible pavement construction, mitigated risks of differential settlement, and achieved a 33% reduction in the volume of imported fill. As this case study shows, the use of geogrids for permanent and temporary roads can help speed up housing and residential projects whilst also reducing costs.
Figure 10 – Value engineered alternative design for an access road at the Orchard Place housing scheme in Norfolk.
How Tensar can help reduce costs through value engineering
You’ll now understand what value engineering is, the benefits, and what each stage of the process entails. We’ve also explained in this guide the importance of value engineering, the formula, and the challenges that could be faced when looking to cut costs without affecting the value of the product.
We can assist you with reducing materials costs while maintaining performance to keep the balance between cost and quality. Our Tensar+ software is not only free to use but can help simplify the analysis in value engineering with pre-calculated and cost-effective solutions. Get started today by requesting a value-engineered solution to clarify the long-term value of using Tensar’s solutions in your upcoming project. This can help with informed decision-making and cost-savings when informing stakeholders.
Tensar provides design support to help reduce the hours you need to spend on value engineering processes.
Get in touch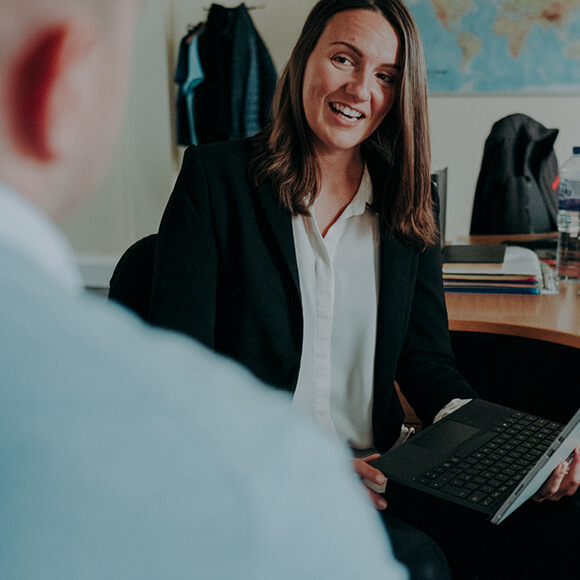